Metal processing can be broadly categorized into two types: cold and hot processing.
The hot processing refers to the processing of materials after they are heated, such as hot rolling, while cold processing involves processing metal at normal temperatures, such as turning, milling, chipping, and grinding.
Cold forming is also a part of cold processing. Although it has been around for a long time, it is still largely an empirical discipline.
Most cold forming techniques are suitable for all metals except for stainless steel, as stainless steel has higher strength and hardenability. Additionally, stainless steel workpieces after cold processing serve both functional and ornamental purposes, making it crucial to protect their surface from damage and rust.
Therefore, special techniques must be employed for the cold processing and production of stainless steel.
Common cold forming methods for stainless steel
In the process of forming stainless steel, two main technologies are utilized: cold rolling and hot rolling. Within the realm of cold processing, there are numerous methods to choose from.
Here is a brief overview of some of the common cold forming techniques for stainless steel:
(1) Cold Bending Forming
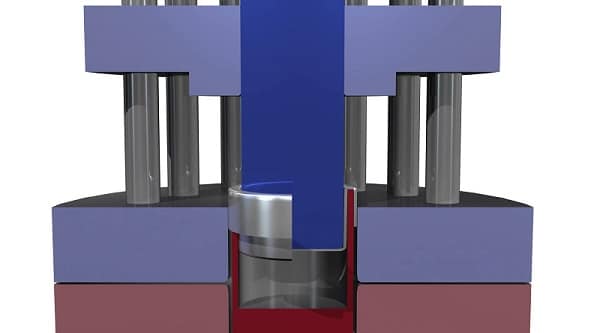
Cold bending is a widely used method in the forming of stainless steel sheets and parts. The punch press is typically an open-type single-moving machine, with mechanical or hydraulic transmission and a long, narrow table.
While the machine is limited to producing linear parts, experienced tool designers can use it to create complex shapes. The length of the parts produced by cold bending presses is determined by the original type and thickness of the stainless steel, the power of the machine, and the size of the installed tools.
For example, some large punch presses, such as an 11-meter standard 900-ton cold bending punch press, can produce austenitic stainless steel workpieces with a length of 9 meters and a thickness of 8.0mm.
To minimize abrasion on the stainless steel, the tools of the cold bending punch press are typically made of 12% chromium, and a plastic film can be used for added protection.
Using the standard mold of a cold bending punch press is cost-effective for small batch production, but if a special mold is required for a specific shape, large batch production is more economical as it reduces the cost of the mold.
With advancements in technology, more and more companies are utilizing cold bending forming technology to produce a large number of parts.
(2) Roll Forming
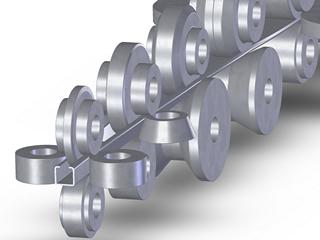
The roll forming method is used to shape stainless steel into complex forms using a series of continuous frames, making it ideal for the production of plates and special-shaped wire.
The roll forming process follows the principle of gradual deformation, with each frame of the roller gradually rolling until the desired product shape is formed. Depending on the complexity of the shape, the process can involve up to 36 frames or as few as three or four.
The rollers are usually made of cold die steel with a hardness of HRC62 or higher. To ensure a smooth finish on the workpiece surface, the roll surface must also have a smooth finish.
Roll forming is most economical for the production of large quantities of long-shaped parts. Conventional plate mills can process strips with a width range of 2.5mm to 1500mm and a thickness of 0.25mm to 3.5mm, while conventional wire mills can process wire with a width of 1mm to 30mm and a thickness of 0.5mm to 10mm. The shapes of the machined parts can range from simple planes to complex, closed sections.
In general, roll forming is only economical when the monthly output of stainless steel sheet is over 30,000 meters or the monthly output of stainless steel wire reaches more than 1000T, due to the high cost of cutting tools, mold processing, and equipment.
For roll forming of either sheet or wire material, it is important to guarantee a smooth finish on the raw material surface and regularly check the mold surface to prevent surface contamination and bruising. The equipment must also be strong enough to handle the hardenability and high rebound margin of stainless steel under cold work.
(3) Stamping Forming
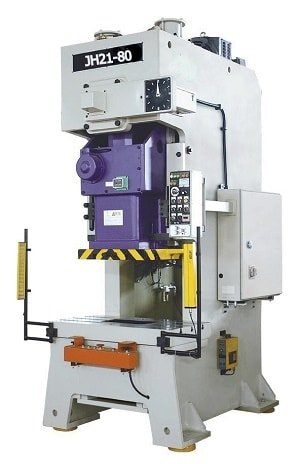
Stainless steel stamping molding uses punches and dies to produce the desired product shape. This technology is commonly used in the production of stainless steel kitchen utensils, such as pots, pens, and handles. The punch press can be either mechanical or hydraulic, but it is recommended to use a hydraulic drive for deep drawing as it provides full pressure throughout the process.
Most traditional technologies can be used for stainless steel stamping forming, but because stamping stainless steel requires over 60% more pressure than low-carbon steel, the press frame must be able to withstand the high pressure.
It is also important to avoid scratches, especially due to the high friction and temperature of stamping stainless steel, which can cause surface scratches on the workpiece.
Specialized stamping oil or lubricating oil with extreme pressure additives should be used instead of soap or emulsion. However, these extreme pressure additives may cause corrosion on the stainless steel surface, so it is important to remove oil stains from the workpiece surface after stamping.
Due to the high cost of stamping die processing, stamping molding is only used for mass production.
(4) Rubber Gasket Forming
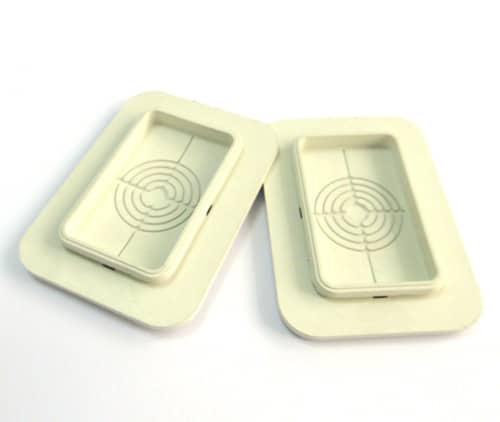
The use of rubber gasket forming technology can significantly reduce mold processing costs and is suitable for small batch production.
The molds used in this technique are made of low-cost materials, such as hardwood or steel epoxy resin as the force piston and rubber gasket as the cavity block.
The rubber can be in the form of a solid rubber block or a laminated rubber block, which is around 30% higher than the forming machine.
When the molding machine is closed, the rubber block compresses the stainless steel blank. When the machine is raised, the rubber gasket returns to its original form and can be reused.
However, rubber gasket molding is limited in its ability to produce complex shapes and has restrictions on the maximum depth of the parts produced. This technique is typically used for small batch production of stainless steel parts with a thickness of less than 1.5mm.
(5) Flanging Forming
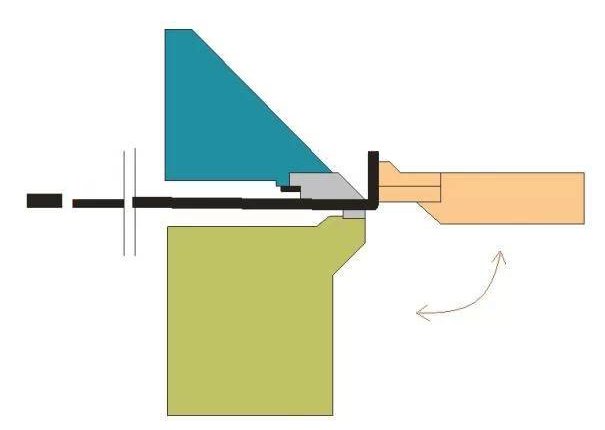
A folding machine is a simple bending machine that can be operated either manually or mechanically.
The simplest method is to use a mold with a bending radius to secure the steel plate firmly on the machine tool worktable, with the protruding part of the material on another workstation. The table can then rotate along the center of the bending radius.
When the table rises, it bends the stainless steel to the desired angle, with the stainless steel sliding on the worktable during the bending process. To prevent scratches on the stainless steel surface, the worktable must have a smooth surface.
In practice, a plastic film is often used to protect the stainless steel surface. The upper beam is usually wedged to form a gap, which can be folded into a quadrilateral box or groove with the appropriate shaped blank.
The flanging machine was once used to produce stainless steel sheet products with large size and simple shape, but these products are now typically produced using cold bending presses.
(6) Cylinder Forming
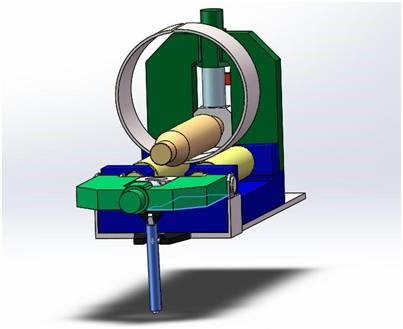
Curved plates are commonly used to produce a variety of thin plate cylinders or cylinder segments.
The traditional rolling machine has a pair of adjustable rollers that can be adjusted based on the thickness of the steel plate. The third roller, known as the bending roller, controls the diameter of the cylinder body.
There is also a variant of this machine that uses three rolls arranged in a pagoda shape. The bottom roller is the driving roller, and the top roller rotates due to the friction between it and the workpiece. The diameter of the bottom roller is typically half that of the top roller.
The minimum diameter of the cylinder produced by these two types of equipment is the diameter of the top roller plus 50mm, while the maximum diameter depends on the size of the material, the rigidity of the machine and parts. In certain cases, the cylinder may need to be supported by frames.
In reality, different products may require a combination of various methods or different processing techniques to achieve the desired quality. Therefore, it is important to have a good understanding of stainless steel cold forming methods to use them effectively.
Common problems and treatment measures in stainless steel cold forming process
(1) The presence of flaws such as dirt, scratches, pits, pitting, or double skin on the surface of roughcast materials can be exacerbated during the cold forming process, leading to a decrease in the quality of the finished product. Therefore, it is important to thoroughly inspect the surface condition of roughcast materials before forming to ensure that they are clean and free from defects.
(2) The formation of dirt, rust, pits, and scratches on the surface of the workpiece can occur when the forming mold and work platform are dirty, and metal fragments are not cleaned in a timely manner. To prevent this, it is important to regularly polish the mold to maintain their cleanliness and to keep the processing equipment and workshop clean.
(3) Some forming techniques involve sliding contact between the metal, which can damage the passivation coating of stainless steel and result in cold welding between the surface of the stainless steel and the tool. This can cause serious scratches on the surface of the stainless steel if the solder is broken during the sliding. To avoid this, it is important to maintain the molding equipment in good condition and to have operators who are skilled and cautious to prevent sliding of the material.
(4) Stainless steel has high strength, and austenitic stainless steel has significant cold hardenability. If the deformation is too large during the cold forming process, it can lead to fracture of the workpiece or damage to the mold and machine equipment. To prevent this, it is important to test the rigidity of the workpiece and maintain a reasonable amount of deformation while ensuring production efficiency and product quality.
(5) After cold forming, the passivation coating of the stainless steel surface can be damaged and contaminated with stamping oil, mold debris, and other metal, which can easily lead to corrosion. To ensure a finished workpiece with good stainless properties and a smooth finish, it is important to clean oil stains and process passivation, and, if possible, protect the surface of the workpiece with a plastic film.
As the demand for stainless steel increases, the use of cold forming technologies for stainless steel is becoming more widespread. It is important to choose the appropriate forming technique based on the features of the product, maximize production efficiency, and reduce production cost to provide consumers with high-quality, affordable stainless steel products.
Very good article. As a stainless steel welder I learned quite a bit